
Typical Flow sheet for Iron Ore Beneficiation

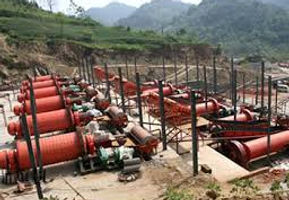
Beneficiation is a process which removes the particle like Alumina, Silica from the Iron Ore. It separates Fe2O3 or Fe3O4 from other impurities in the iron ore. In this process the Fe content is improved to maximum possible extent. The highest can be around 70%.
Iron ore is a mineral which is used after extraction and processing for the production of iron and steel. The main ores of iron usually contain Fe2O3 (70 % iron, hematite) or Fe3O4 (72 % iron. magnetite). Ores are normally associated with unwanted gangue material. Grade of iron ore is usually determined by the total Fe content in the ore. Run of mines ores after dry or wet sizing, if contains greater than 62 % of Fe, are known as ‘natural ore’ or ‘direct shipping ore’ (DSO). These ores can be directly used in the production of iron and steel. All other ores need beneficiation and certain processing before they are used in the production of iron and steel.
Low grade iron ores cannot be used as such for the production of iron and steel and need to be upgraded to reduce its gangue content and increase its Fe content. The process adopted to upgrade the Fe content of iron ore is known as iron ore beneficiation (IOB).
However, Iron ores from different sources have their own peculiar mineralogical characteristics and require the specific beneficiation and metallurgical treatment to get the best product out of it. Also for effective beneficiation treatment, effective crushing, grinding, and screening of the ore is necessary for which suitable crushing, grinding, and screening technologies are to be employed. The choice of the beneficiation treatment depends on the nature of the gangue present and its association with the ore structure. Several methods/techniques such as washing, jigging, magnetic separation, gravity separation, and flotation etc. are used to enhance the Fe content of the Iron ore and to reduce its gangue content. These techniques are used in various combinations for the beneficiation of iron.